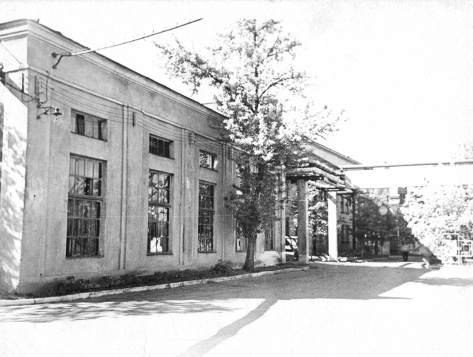
- The enterprising factory owners E.A. Bosse and R.G. Genefeld bought two tens of acres of land from the landowner and mine owner Rutchenko and built an iron foundry near Grigorevka village. The first fifty workers were recruited from the peasantry. The factory was a semi-artisanal workshop with one iron foundry. The workshop made mine headframes, small boilers and forgings.
- There was an industrial revival in the Donbass. A new foundry was erected, the pattern shop and mechanical shop were expanded, and a heating furnace was added to the forge. 200 workers.
- Bosse’s factory is called the “Machine and Ironworks”. Here the production of small steam and manual winches, pumps, fans with manual drive, crushers, stands and carriages was mastered. The number of workers exceeded 300.
- The number of workers and employees was 319. The factory reached its pre-war capacity and was officially called the State Machine Works.
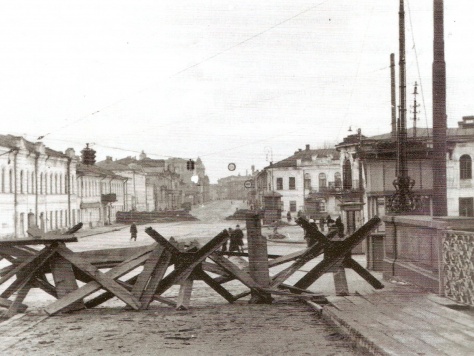
- About 2 thousand workers were employed at the plant. The mechanical workshop was built, construction of the new assembly shop began, a hospital and a canteen were opened in the factory settlement.
- The plant was named after “The 15th anniversary of Komsomol of Donbass”.
- Since the restoration of the plant the mines of Donbass received 1,503 hoisting machines and winches, 162 roof supports, 54 head frames, 329 head blocks. The plant rebuilt 58 hoisting machines and 20 winches directly at the mines.
- The forging shop, a large bay of mechanical shop No. 5, the first stage of the foundry shop and the factory administration building were built.
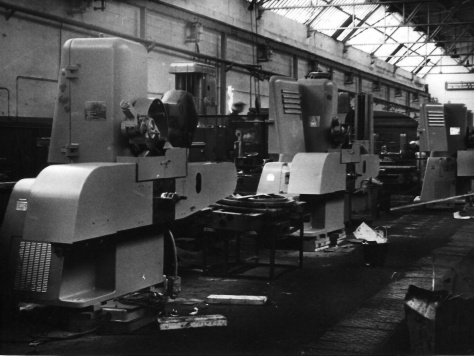
- On the basis of the plant’s engineering services, a research, design and technological institute for coal and mining engineering – NIPKTIuglegormash – was established.
- The installation of the mechanical part of the VOD-30M2 fan in Egypt was completed with the participation of the plant’s specialists. The order for manufacturing of two more fans was received.
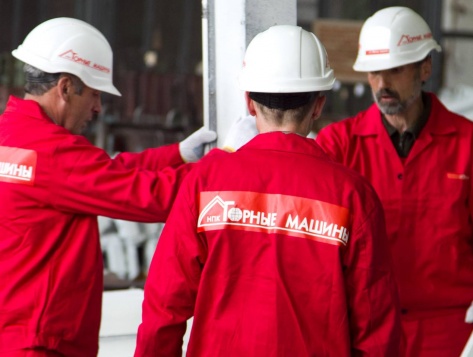
- Consolidation of SCM’s machine-building assets. Creation of the machine-building holding Ukruglemash. In 2006 it was renamed to Mining Machines.
- Donetskgormash JSC as part of SIC “Mining machines”.
- Druzhkovka Machine Building Plant became part of SIC “Mining machines”.
- Development and introduction to the market of a new technical level of longwall equipment and tunnelling equipment (UKD300, KDK500, KSD27, KSD26V, KDD, DT, KPD, BPR, KTPV, SND300)
- Supply of 3 ANShch winning assemblies to Vietnam.
- Supply of 6 KPD roadheaders to Vorkutaugol.
- Supply of 11 fans VRTsD-4.5 to Uralkali JSC and Silvinit JSC
- Supply of 6 VTsD31.5 fans for ArcelorMittal Temirtau
- Supply of 3 Poisk mining machines to Colombia.
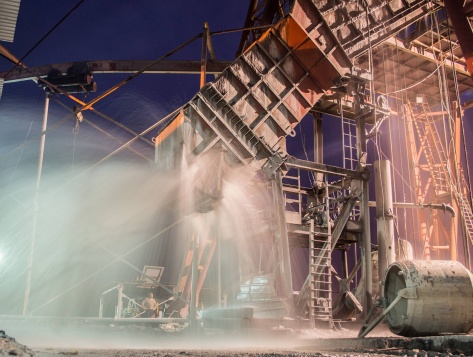
- Development and approval of the Company’s Development Strategy.
- Opening of a representative office in Vietnam and signing of a contract with the Vietnamese company VINACOMIN on the construction of mine shafts.
- Transition to a divisional management structure for the company’s products.
- Opening of specialized repair facilities in Gorlovka – for the repair of coal shearers and in Druzhkovka – for the repair of powered roof supports
- Creation of a specialised service company.
- Regulation and standardization of all processes in the company.
- Merger with the company of the Kharkov machine-building plant “Svet Shakhtera”.
- Supply of modernized rotor installations for Bucket-wheel excavators to the Gacko open pit (Bosnia and Herzegovina).
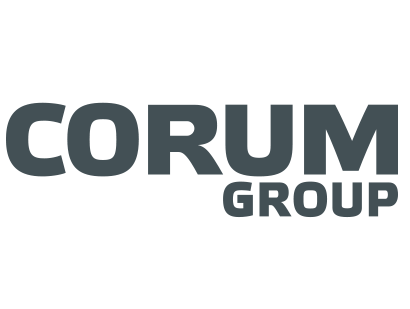
- Conclusion of an agreement on the Strategic Alliance with DTEK.
- Introduction of a new progressive payment system in the company.
- Opening a permanent office in Poland.
- The company was renamed as Corum Group.

- Company adopted the Code of Corporate Ethics.
- Corum and Metinvest Group concluded a Strategic Alliance agreement for a period of five years.
- Company signed a declaration of intent to establish a joint venture in China.
- Corum incorporated enterprises “Minespecialbuild” and “Luganskgiproshakht”.
- The assembly sites were opened on the basis of the plants “Corum Svet Shakhtera” and “Corum Druzhkovka Machine-Building Plant”.
- The new KBT200 was launched on the market – the world’s first shearer with vertical drum-type operating devices and a chainless feed system.
- The main office of the company moved to Kiev.
- The first 2 roadheaders were supplied on the market of Poland.
- The Corum winder set its first record at the mine named after Geroev Kosmosa.
- Construction of two mine shafts in Vietnam was completed.
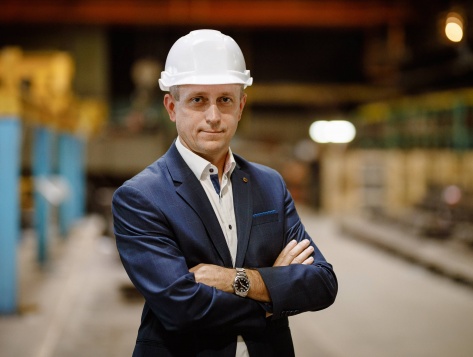
- Built a centralized procurement system.
- Reduced and improved the quality of the working capital.
- Invented and implemented the project “School of internal coaches”.
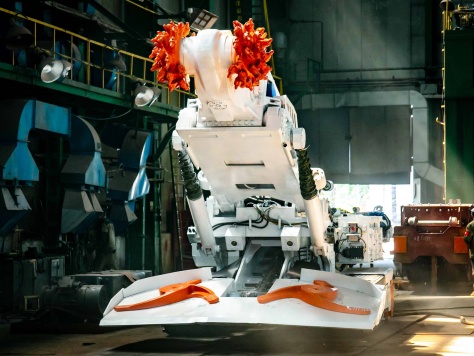
- Increased the transparency of the sales process and changed the approach to them. As a result, the volume of contracts concluded in 2016 increased by 32% compared to 2015.
- 62 coaches, who developed 80 training programs, were qualified.
- Implemented an institute of mentoring to fill the shortage of workers at enterprises and improve their skills.
- Built a fast decision-making system.
- Reduced the production time of the KPD roadheader production to 100 days. In 2015, it took 210 days.
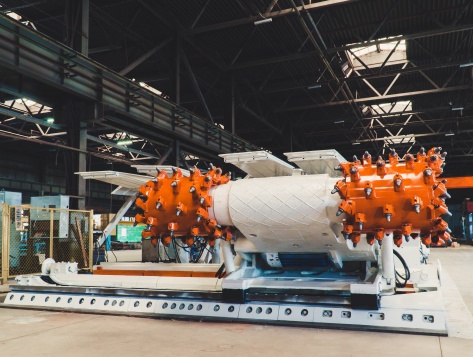
- Created the world’s first roadcutter system KNF, which has already been tested and is produced on a large-scale basis.
- Upgraded the heavy support 3KD90TC, and tripled its resource.
- Brought to the market a completely new development – a CLS450 shearer.
- Completed the construction and reinforcement of the shafts of the Nui Beo Mine in Vietnam.
- Established two divisions in the area of service and repair.
- Reduced the repair terms of the Client’s equipment in 3 times.
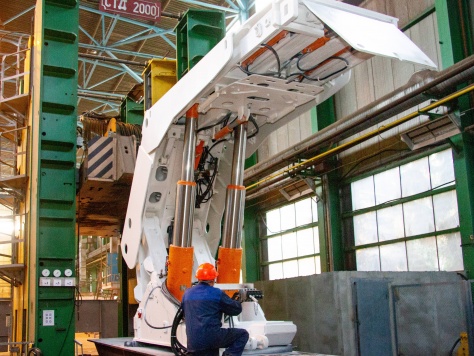
- Supply of three sets of powered roof support ZRP15/35 for Poland
- Corum Group has become a separate machine-building business unit within the largest energy holding DTEK Energo.
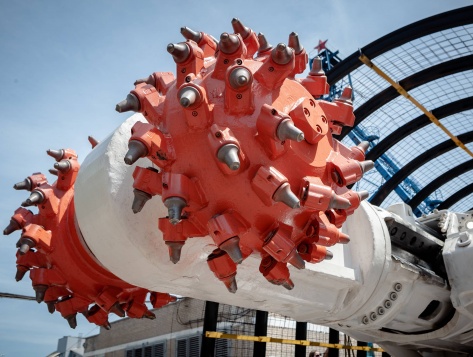
- Corum Minespecialbuild shaft workers set a company record for mine workings. For one month, miners have built 202 meters of ventilation drift of the 9th southern longwall of the block No. 10 of the Pokrovskoye mine administration.
- A new RH160 roadheader was developed and manufactured.
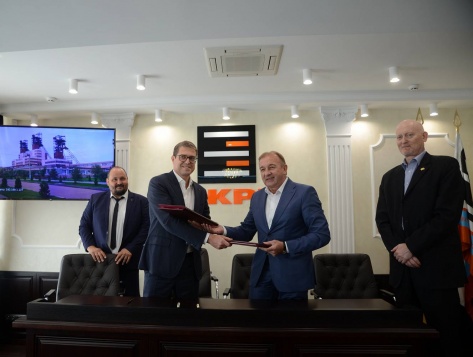
- A major contract was signed between Zaporizhzhya Iron Ore Plant and Corum Minespecialbuild. Corum Group will build and equip a new production site for ZZRK – South Ventilation Shaft No. 2.
- Developed and brought the CLS550P shearer to the market.
- Signed a memorandum of long-term cooperation with Alta.
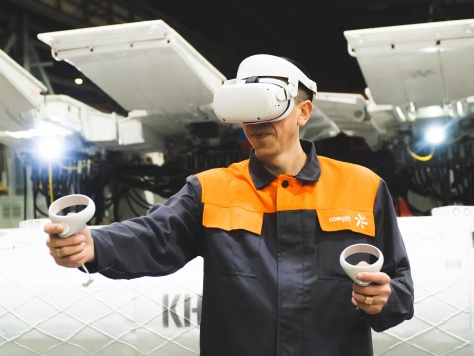
- The first contract for a pilot supply of 17.5/28 KD90T roof support sections was signed with Imbat Madencilik, a leading coal mining company.
- Introduced Company Development Strategy till 2030.
- Launched a pilot project to introduce 5G, Preactor, Expert Technology at Corum Svet Shakhtera.
- Customer confidence and NPS rate of the company increased to 53%.
- Developed and implemented KTPV-EP-1000/6 power train.